The story of powder evaluation - Part 2
In the previous report, we discussed the evaluation of metal powders. In the powder metallurgy industry, the process of kneading (mixing main raw material with sub materials) is unavoidable. This time, we will move on to the kneading stage.
Art of material mixing
Metal powder and resin powder are kneaded to make feedstock in pellets shape for injection moulding. The amount of resin is an important factor to control not only the fluidity of the injection moulding process, but also the dimensional accuracy of the final component. The optimum amount of resin to metal powders of various particle sizes must be not too much nor too little, and the method of determining the resin amount, the method of kneading and evaluating the degree of mixing, is an area of advanced know-how.
Actual resin content
The ideal form of feedstock is each metal powder is covered thin layer of resin homogeneously and independently dispersed. Therefore, the surface area of the metal powder is important for determining the optimal amount of resin. The BET theory gas adsorption measurement is the standard method for calculating the surface area per unit mass of powder, but as mentioned in the previous report, here we would like to put aside difficult theory and introduce a more on-site, we will talk about the analog method of measuring, the flaxseed-oil adsorption method. This method allows you to feel the surface area of the powder with your own eyes and hands. Oil adsorption is an evaluation method for pigments or powder properties from surface area view point, specified as JIS K5101-13-1:2004 (ISO 787-5:1980). A few drops of oil is added to the powder and mixed homogeneously using a spatula. The endpoint is determined when the powder becomes a complete murshy chunk.
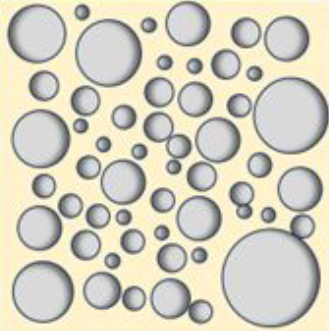
The photos below show the change in appearance during the oil adsorption test using stainless steel powder. Starting from (1), a drop of oil is gradually added and a small lump begins to form little by little from the dry state, approaching the end point around (4). Then, with the next drop from (4) to (5), a dramatic change occurs, and it becomes a complete murshy lump. It is rather magnificent! At this moment, you can feel that the entire surface of the powder has been wetted with oil, which is much more gratifying than just looking at the numbers on the screen. The right graph shows the relationship between the average particle diameter and oil adsorption of 5 different stainless steel powder we use in serial production. The amount of oil adsorption decreases as the particle diameter increases, but also significant differences are observed according to the minor composition change among stainless steel series. This intuitive test gives us a guideline for the optimal amount of resin that is useful for MIM manufacturing.
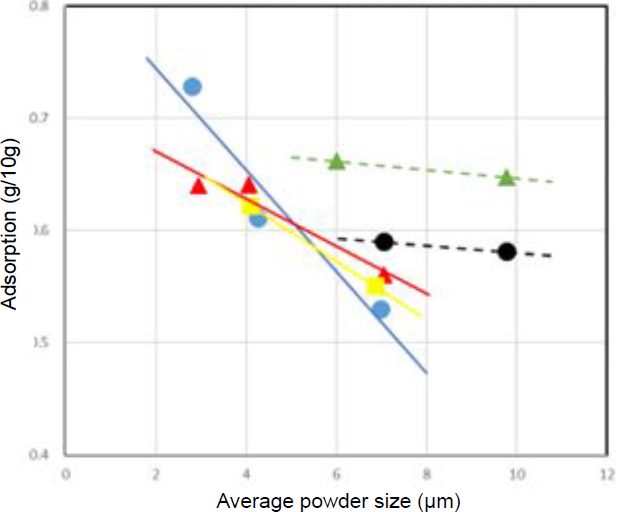

Once the mixing amounts of metal powder and resin are determined, they are kneaded and processed into pellets. In the next issue, we will talk about how to evaluate the degree of kneading.
Download the PDF file
Conclusion
Cracking, slumping or blistering is commonly observed due to the binder swelling and/or residual stress difference between the surface and interior. It is possible to avoid these problems by selecting appropriate organic solvents and temperature control.
The catalytic deboning uses sublimation of binder, thus it is possible to decompose the binder in relatively short processing time with minimizing the deformation. However, with a strong acidic atmosphere, theapplicable metal material option is limited.
In the sintering process, the necking, which is bridging the metal powders by thermal diffusion, starts at the sintering temperature. Once the necking starts, the shrinking is observed and increases the density, thus before starting the necking reaction, all the organic components should be decomposed and gas between the powders should be removed. In the sintering process, the unwanted chemical reaction, such as oxidation or carbonization, leads to mechanical property loss, therefore a precise atmosphere control with low heating rate at the beginning of the process is required. Also, when it reaches the sintering temperature, some add it vegetal can be evaporated.