It's been a while since the "I want to know but can't ask” series. We will discuss the basics, realities, and concerns of powder, which serve as the starting point for manufacturing, not only in the MIM industry but also in various other industries, over several issues.
How much powder particles are we handling?
Now, let's start with a rough calculation. The powder we often use, with an average particle size of about 8 μm, has approximately 2 billion particles per cubic centimeter. If we use 5 kg of powder in feedstock manufacturing, assuming the density of stainless steel is 7.8 g/cm3, there will be around 1.25 trillion particles in that amount. Moreover, no two particles are the same.
While the world's population is around 8 billion, MIM manufacturing operates with a collective of particles that is 150 times that number. Similar to humanity, MIM manufacturing deals with troublemakers occasionally, creating products while grappling with these challenges.
Powder evaluation
The feedstock, a crucial element in MIM manufacturing, is created by heating and blending metal powder and resin powder, forming a clay-like mass as shown in the photo below. This mass is then processed into pellet form, referred to as feedstock. The desired-shaped molded body is produced by injecting this feedstock in the injection molding process. While resin powder is essential, its evaluation is challenging and it does not persist in the final product. Therefore, in MIM, the focus is primarily on evaluating metal powder.
When evaluating powder, there are chemically static evaluations of the powder itself, such as its shape, size, and particle size distribution. There are also chemically dynamic evaluations when the powder is mixed with some dispersing medium and used in actual processes. In the case of MIM, the resin powder serves as the dispersing medium, and the results of the chemically static evaluation significantly impact the formability during molding.
There are also chemically dynamic evaluations when the powder is mixed with some dispersing medium and used in actual processes. In the case of MIM, the resin powder serves as the dispersing medium, and the results of the chemically static evaluation significantly impact the formability during molding.
When purchasing metal powder, the mill sheet provides information on chemical composition, particle size distribution (average particle size, D50 value), and tap density. Tap density is the most convenient evaluation item when assessing powder as a mass, along with the angle of repose. These results, including bulk density, serve as indicators predicting powder fillability, blendability, and flowability.
On the other hand, particle size distribution is the most important information when handling powder. There have been various methods for measuring this, but it is no exaggeration to say that optical measurement methods using lasers are the mainstream these days. The device itself is expensive and complicated, but the actual measurement process is to put a sample about the size of an earpick (approximately 0.1 g) into the cell, so it may be the best in terms of simplicity. What's more, it is extremely useful because it instantly shows a ‘’beautiful“ distribution and average particle size as shown in the figure above. Even though you might feel a bit uneasy about assessing the powder that is purchased in 25kg lots at just 0.1g, the ratio is 4 ppm, the SEM photo on the right above shows that all of the powder is actually of a good quality. (To be continued)
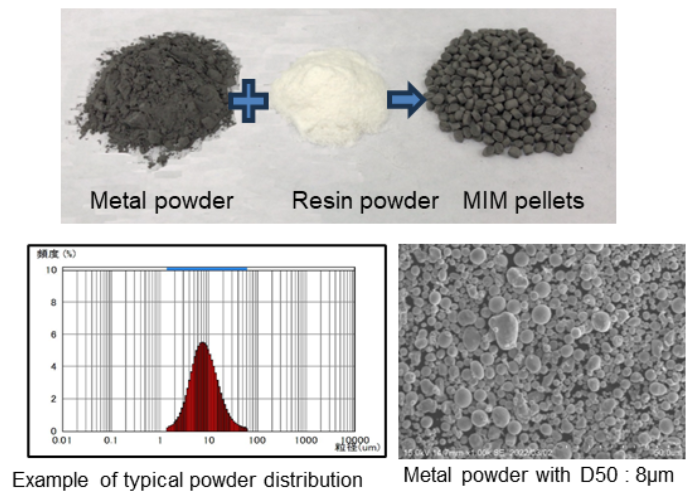
We will exhibit at the MD&M West 2024 in Anaheim, California, USA between 6th and 8th February 2024 at Booth #432 in Hall E at the Anaheim Convention Center. Please come and visit our stand at MD&M West!
Greetings from Osaka, Japan
Hi, I am Yukino Matsusue in Production Control Department. I joined the company in April 2023, and now learning how to calculate the cost of production and to plan a prototype project etc. I am glad when the projects go smoothly as we planned and when we receive order for the quotation I took part in cost calculation. I try to enjoy my work on daily basis and at the same time, to pay attention to details.
My hobby is to eat delicious food, especially sweets and I really enjoyed eating different kinds of gelato in summer. My favorite are pistachio and raspberry flavors.😋 Recently, I got to experience the Osechi (Japanese traditional food for the new year days) with sweets, which was very tasty.
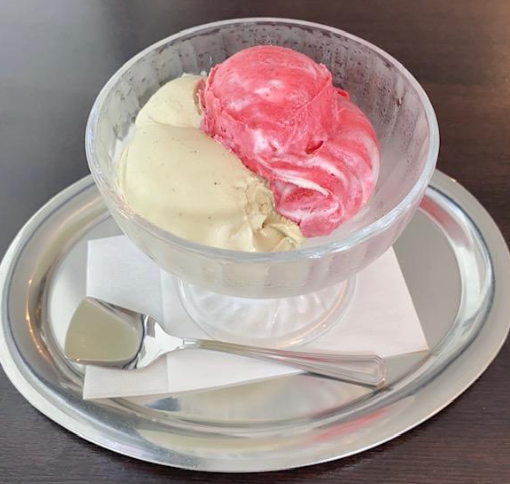
Download the PDF file
Conclusion
Cracking, slumping or blistering is commonly observed due to the binder swelling and/or residual stress difference between the surface and interior. It is possible to avoid these problems by selecting appropriate organic solvents and temperature control.
The catalytic deboning uses sublimation of binder, thus it is possible to decompose the binder in relatively short processing time with minimizing the deformation. However, with a strong acidic atmosphere, theapplicable metal material option is limited.
In the sintering process, the necking, which is bridging the metal powders by thermal diffusion, starts at the sintering temperature. Once the necking starts, the shrinking is observed and increases the density, thus before starting the necking reaction, all the organic components should be decomposed and gas between the powders should be removed. In the sintering process, the unwanted chemical reaction, such as oxidation or carbonization, leads to mechanical property loss, therefore a precise atmosphere control with low heating rate at the beginning of the process is required. Also, when it reaches the sintering temperature, some add it vegetal can be evaporated.