μ-MIM® Technical Newsletter Vol. 35: The renovated headquarter in Japan
We have recently renovated our headquarters’ factory: at the beginning of this year, we started the renewed factory operation. Some of the measurement or evaluation equipment installation is not completed yet though we will introduce our new production line.
HQ main building
Taisei Kogyo was established in 1972 as a plastic injection moulding manufacturer.
On the ground floor of our HQ building, there were huge plastic injection moulding machines, such as the 220t class before. However, it has been a while since we shifted our main business to MIM, and we focus on small complex designed metal component serial production. Thus, we have changed to smaller injection machines with precise injection parameter control systems. Also, we applied a positive pressure ventilation system to the new injection moulding room. Since we have more small component production requests, the tiny contamination in the air can reduce our component quality. This new positive pressure ventilation system will help our quality control even better than before. Additionally, the new injection moulding room has an under-floor infrastructure. Thus, making it easier to relocate the injection moulding machine with a safer working environment.
Also, on the ground floor in our main building, there is another section for X-ray CT. As we informed you before, we transfer our X-ray CT from our R&D room in Higashi-Osaka, which is around 30 min drive distance. The X-ray CT room requires different temperature control from the injection moulding room, thus separated but next to each other to increase the quality control efficiency. In this X-ray CT room, there is also the SEM. A more highly reliable instant tolerance inspection has been realised.
The upper floor of our main building is the quality inspection room and working space. The production team and quality control team are located very close to each other; thus our quality serial production will be pledged stronger.
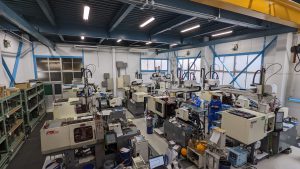
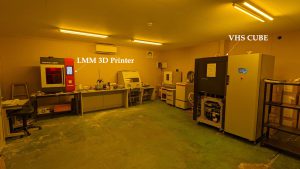
PM building
There is another building, called the PM (powder metallurgy) building. When we established our MIM production line, the debinding and sintering furnace was only used for MIM, not in plastic injection moulding at all. Therefore, the furnace or kneading facilities were settled in this building, and it was called that. In a part of the PM building, we have constructed a 3D printing yellow room. In this room, we have a Lithography-based Metal Manufacturing (LMM) 3D printing machine from Incus GmbH and 3D printing related facilities. Also, there is a newly installed prototype furnace, VHS-CUBE from Shimadzu Industrial Systems. In this room, we are capable of completing the whole prototype production without risking the lithographic exposure.
Building 4
Previously we organised the production lines in building 4. Now most of the injection machines move to our new injection moulding room, thus we have got more space in building 4. We are considering arranging our evaluation equipment enhancement here.
Our future target
We have been working hard to maintain our quality assurance level to satisfy the ISO13485 requirement and above that we have been working even hard to answer our customers’ requirements. Since the regulation will be changed frequently especially in the medical industry, we will keep upgrading our ability. We are installing the data control system for our quality assurance, and we look forward to reporting you completing the installation.
Column
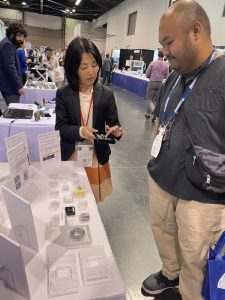
Between 12th and 14th April 2022, we attended the MDM (Medical Design & Manufacturing) West in Anaheim, California in the USA as a member of the Micro Manufacturing Association of Japan. It was the second time for us to attend the exhibition in this way, that is, in collaboration with other Japanese companies who are specialized in micro technology of various kinds.
People were so excited about the face-to-face event, which is one of the first in the post-pandemic time. Many people were very impressed when they saw our MIM components samples, commenting “Wow, I never imagined that you can make such small and precise parts with MIM technology!”.
Next exhibition this year will be at Micronora in Besancon, France between 27th and 30th September 2022. We hope to see you there!
Conclusion
Cracking, slumping or blistering is commonly observed due to the binder swelling and/or residual stress difference between the surface and interior. It is possible to avoid these problems by selecting appropriate organic solvents and temperature control.
The catalytic deboning uses sublimation of binder, thus it is possible to decompose the binder in relatively short processing time with minimizing the deformation. However, with a strong acidic atmosphere, theapplicable metal material option is limited.
In the sintering process, the necking, which is bridging the metal powders by thermal diffusion, starts at the sintering temperature. Once the necking starts, the shrinking is observed and increases the density, thus before starting the necking reaction, all the organic components should be decomposed and gas between the powders should be removed. In the sintering process, the unwanted chemical reaction, such as oxidation or carbonization, leads to mechanical property loss, therefore a precise atmosphere control with low heating rate at the beginning of the process is required. Also, when it reaches the sintering temperature, some add it vegetal can be evaporated.