μ-MIM® Technical Newsletter Vol. 26: Paper review; AM co-researching work using FDMet
We have published literature to Materials, regarding the FEMet additive manufacturing, with Prof. Hiroshi Ito, Graduate School of Organic Materials Science, Yamagata University, in May 2020 and Jan 2021. In this issue, we will introduce an overview of those researching work.
Background
Metal additive manufacturing (Metal AM) realises any design of forming from 3D-CAD data as we published the technical newsletter before. There are various method of forming the component in metal AM, but in our co-researching work, fused deposition of metals (FDMet) is deployed. The FDMet employs filament for forming material, which has a diameter of 1.7 mm wire shape. This filament is made from metal powder and binder mixture and Micro MIM Japan and Taisei Kogyo were responsible for this filament development.
Forming parameter and mechanical properties
It is well known that any type of metal AM components have anisotropy properties. In these papers, the clear relationship between the layer stacking direction, layer thickness and tensile properties. The stacking layer is perpendicular to the tensile direction, the tensile strength is lower than the stacking layer is parallel to the tensile direction. Also 0.1 mm the layer thickness specimen gives higher density and mechanical strength than the 0.3 mm specimen.
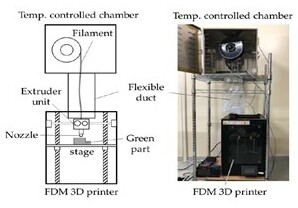
(T. Kurose et al., Influence of the Layer Directions on the Properties of 316L Stainless Steel Parts Fabricated through Fused Deposition of Metals,Materials)
Feedstock effects
Unlike the MIM process, there is no compaction process of the feedstock in the FEMet, therefore, the filament properties affect significantly the mechanical properties in the final sintered component. In these researches, 2 types of stainless steel (316L and 17-4PH) with the powder size distribution class were deployed. However, the density is increased in 17-4PH paper even the FEMet parameters were the same as the 316L work. This is due to our filament development. The density increment will lead to mechanical property improvement surely in the metal AM process. In FDMet filament, it is required not only the density improvement but also the the processability, chemical and physical stabilities. Our µ-MIM® technology will enhance the possibility of the Metal AM manufacturing field too.
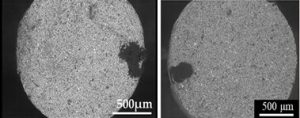
(Left; T. Kurose et al., Influence of the Layer Directions on the Properties of 316L Stainless Steel Parts Fabricated through Fused Deposition of Metals,Materials
Right; Y. Abe et al., Effect of Layer Directions on Internal Structures and Tensile Properties of 17-4PH Stainless Steel Parts Fabricated by Fused Deposition of Metals.)
Reference
Influence of the Layer Directions on the Properties of 316L Stainless Steel Parts Fabricated through Fused Deposition of Metals,Materials, 13, 2493, 12 pages, (2020).
DOI: 10.3390/ma13112493
Effect of Layer Directions on Internal Structures and Tensile Properties of 17-4PH Stainless Steel Parts Fabricated by Fused Deposition of Metals. Materials,14, 243, (2021).
DOI: 10.3390/ma14020243
Webinar
Please keep the 7th of April Time: 13:30 German time, 18:30 Thailand time, 20:30 Japanese
time free for our μ-MIM® technology webinar. We will send you the link to the webinar prior to the event.
Column
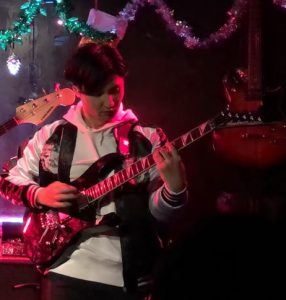
Hello. I am Nakagawa from the quality control department. I am responsible for optical dimensional measurement in both trial and mass production. I started playing the guitar 2 years ago and foam my own band to play rock music. Unfortunately, my band already broke up and now I am interested in jazz and blues. I am practising hard to be able to enjoy jazz and blues and whenever I could play the new phrase, the music makes my heart sing. Also whenever I could measure the difficult specimen, I feel delightful.
Conclusion
Cracking, slumping or blistering is commonly observed due to the binder swelling and/or residual stress difference between the surface and interior. It is possible to avoid these problems by selecting appropriate organic solvents and temperature control.
The catalytic deboning uses sublimation of binder, thus it is possible to decompose the binder in relatively short processing time with minimizing the deformation. However, with a strong acidic atmosphere, theapplicable metal material option is limited.
In the sintering process, the necking, which is bridging the metal powders by thermal diffusion, starts at the sintering temperature. Once the necking starts, the shrinking is observed and increases the density, thus before starting the necking reaction, all the organic components should be decomposed and gas between the powders should be removed. In the sintering process, the unwanted chemical reaction, such as oxidation or carbonization, leads to mechanical property loss, therefore a precise atmosphere control with low heating rate at the beginning of the process is required. Also, when it reaches the sintering temperature, some add it vegetal can be evaporated.