β-Titanium alloys by MIM manufacturing
β-Ti (Beta Titanium) alloys have received a lot of attention as the next generation implant material in medical industry. In this issue, we introduce the reasons of β-Ti alloys attract attentions and our progresses of MIM process development.
What is β-Titanium?
In the 1950s, Ti started deploying and consuming in the aerospace industry because of its low relative weight and high strength. It still the aerospace industry has the largest share of consuming Ti today, however, the medical industry consumption has increased due to its high corrosion resistance, recently. As people's average life expectancy increases and the implants are also required long product life to improve their QOL, thus, the high corrosion resistance property of Ti is attracting attention.
On the other hand, Ti is also known as a hard to process material thus, small complex designed Ti parts are limited. Ti has multi crystalline structure, such as α (alpha) phase and β (beta) phase, which presents the properties of strength and ease of processing, respectively. As for pure Ti, since the α phase is the most stable phase in the room temperature (RT), thus fully α phase structure is observed. Then, to improve its processability, the β phase should exist in the RT, however, the β phase is not stable in the RT thus, need to add some β stabiliser material, such as molibdenum, vanadium. The most well known Ti alloy, Ti6Al4V were developed as a α + β type alloy.
The β phase improves its processability but also lowers the modulus of elasticity. The low elastic modulus means lower ability of elastic deformation and it is a major reason why Ti alloys have caught people’s attention as next-gen implants. It sounds opposite but high elastic modulus material implant gives higher opportunity of breaking original bones. Therefore, the use of β-Ti alloys with low modulus of elasticity in implants would be expected to reduce the likelihood of fracture.
Difficulty of manufacturing Ti parts by powder metallurgy
Powder metallurgy manufacturing, including the metal injection moulding (MIM), requires to have the sintering process to increase the metal parts density. The sintering process uses diffusion bonding reaction among the metal powders and the sintering temperature is lower than the melting point. For example, Ti64 alloy melting point is approx. 1,650°C, and the sintering temperature is around 1,100°C. Compared with casting, powder metallurgy sintering temperature is lower, yet, Ti becomes highly chemically active, and especially reacting with carbon and oxygen, it creates Ti carbide and Ti oxide. As these compounds deteriorate mechanical properties, thus the sintering process should held under perfectly controlled atmosphere, such as high vacuum atmosphere.
MIM feedstock has a higher binder volume ratio as a carbon source than the other powder metallurgy methods and also smaller size metal powder tend to be deployed, that is increase the relative surface area. These facts are enhance the Ti-MIM manufacturing difficulty even more, thus, only a limited number of MIM manufacturers are able to mass-produce Ti parts. Taisei Kogyo Co., Ltd., our manufacturing group company, has realised stable mass production of MIM components made of commercially pure Ti and Ti64 alloys, and also we have focused on developing the β-Ti (a higher ratio of β phase than Ti64 alloy) stable manufacturing.
Development of β-Ti alloy MIM manufacturing
As for materials used as implant, it is required not to use elements suspected of causing allergies or specific diseases, however, there are unfortunately some suspicions of both aluminium and vanadium, which is applied for well known Ti64 alloy.
Thus, β-Ti alloy development is remaining some material development field. For example, molybdenum and chromium have been considered as alternative elements of β stabiliser.
Beside the material development, β-Ti manufacturing development should deal with some limitations. 1st is lower carbon solid solution limit than α phase and 2nd is cooling speed. The low C solid solution limit of the β phase is leading precipitate C at grain boundaries, thus it is required even higher level of controlling the conditions of debinding & sintering than pure Ti and Ti64 alloys. Also, β-Ti with good mechanical property is obtained by rapid cooling, thus many sintering at printing type metal additive manufacturing is researched and published.
Taisei Kogyo Co., Ltd. is now introducing a new sintering furnace and a powder manufacturing equipment to realise the β-Ti alloy MIM manufacturing, so please stay tuned to our further announcement.
Reference; 1)A New Path for Advanced Titanium Alloys in the EU Medical Device Supply Chain. Metals 13(2), 372 (2023). https://doi.org/10.3390/met13020372
2) Effect of Mo Additions on the Physical, Mechanical and Corrosion Properties of CP-Ti Fabricated by MIM. Met. Mater. Int. (2023). https://doi.org/10.1007/s12540-023-01454-2
Greetings from Osaka, Japan
I am Yota Ishihara, a member of Micro MIM Japan Holdings Inc. and Taisei Kogyo Co., Ltd. I am in charge of debinding & sintering processes control and digitization of forms and other documents that are used in our process control. My mottos are to respect people who have the skills that I don’t have and to tackle what others won’t.
On weekends, I join outdoor meetups of a club that I have belonged to since half a year ago. At the beginning of May, we climbed up Mt. Myokensan in Osaka and had a nice BBQ time on the peak.
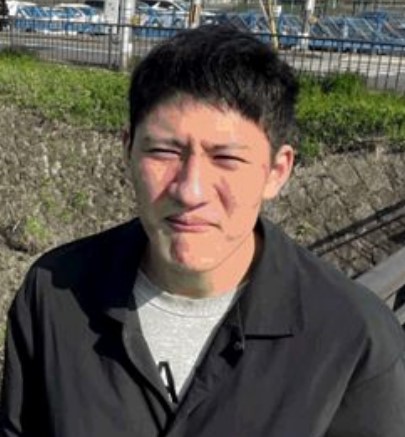
Download the PDF file
Conclusion
Cracking, slumping or blistering is commonly observed due to the binder swelling and/or residual stress difference between the surface and interior. It is possible to avoid these problems by selecting appropriate organic solvents and temperature control.
The catalytic deboning uses sublimation of binder, thus it is possible to decompose the binder in relatively short processing time with minimizing the deformation. However, with a strong acidic atmosphere, theapplicable metal material option is limited.
In the sintering process, the necking, which is bridging the metal powders by thermal diffusion, starts at the sintering temperature. Once the necking starts, the shrinking is observed and increases the density, thus before starting the necking reaction, all the organic components should be decomposed and gas between the powders should be removed. In the sintering process, the unwanted chemical reaction, such as oxidation or carbonization, leads to mechanical property loss, therefore a precise atmosphere control with low heating rate at the beginning of the process is required. Also, when it reaches the sintering temperature, some add it vegetal can be evaporated.