Announcement: Introduction of new equipment
This year marked a strengthening of the global economy's recovery from the pandemic. We thank you all for your continued support. This time, we would like to introduce two equipment that has been introduced newly to our μ-MIM® technology development.
1. Dry electropolishing machine (DLyte)
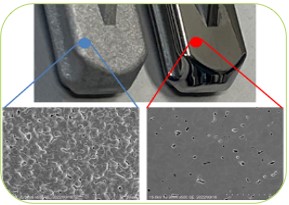
You might have wondered first if “dry” electropolishing machine is really true, but surprisingly yes it is! This electropolishing is performed through a special conductive porous resin ball with a little amount of water instead of electrolyte.
Compared with conventional wet electropolishing, this dry electropolishing has the outstanding features as follow: 1. easy handling, 2. eco-friendly design thanks to the free-electrolyte feature, 3. sharp clean edges.
The picture above shows a processing example of our titanium components. After ca. 30 minutes of processing, as you can see, the surface gets finished shiny. We hope that this machine will be useful for polishing small quantities of exterior components.
2. Compact ultrasonic atomiser (ATO Lab)
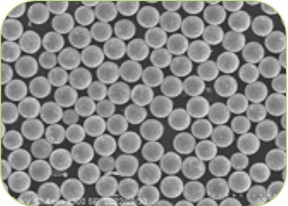
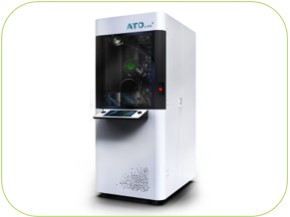
You might have wondered again if “ultrasonic” atomiser is really true. Generally, atomisers for powder production spray water or inert gas over the molten metal.
On the other hand, the ATO Lab as you can see the picture at the bottom, refines metal powder in the following way; First, a wire or a rod is melted by the TIG arc, forming a molten pool on the cooled copper tip. Secondly, ultrasonic shakes the molten pool and makes the liquid surface jump. Finally, the liquid metal rounded by the surface tension is blown off to refine highly spherical metal powder.
This atomiser is targeted at fabricating a small quantity of homogeneous metal powder for the additive manufacturing (AM, e.g. 3D printer), and the synergy effects with our LMM (Lithography-based Metal Manufacturing) 3D printer are expected.
The first polishing machine is from Spain and the second atomiser machine is from Poland.
We have always been looking to the world to collect and disseminate the latest technology information and do our best to provide you with the best products and services. We look forward to working together with you to bring more great metal components for your company from concept to creation.
Exhibition
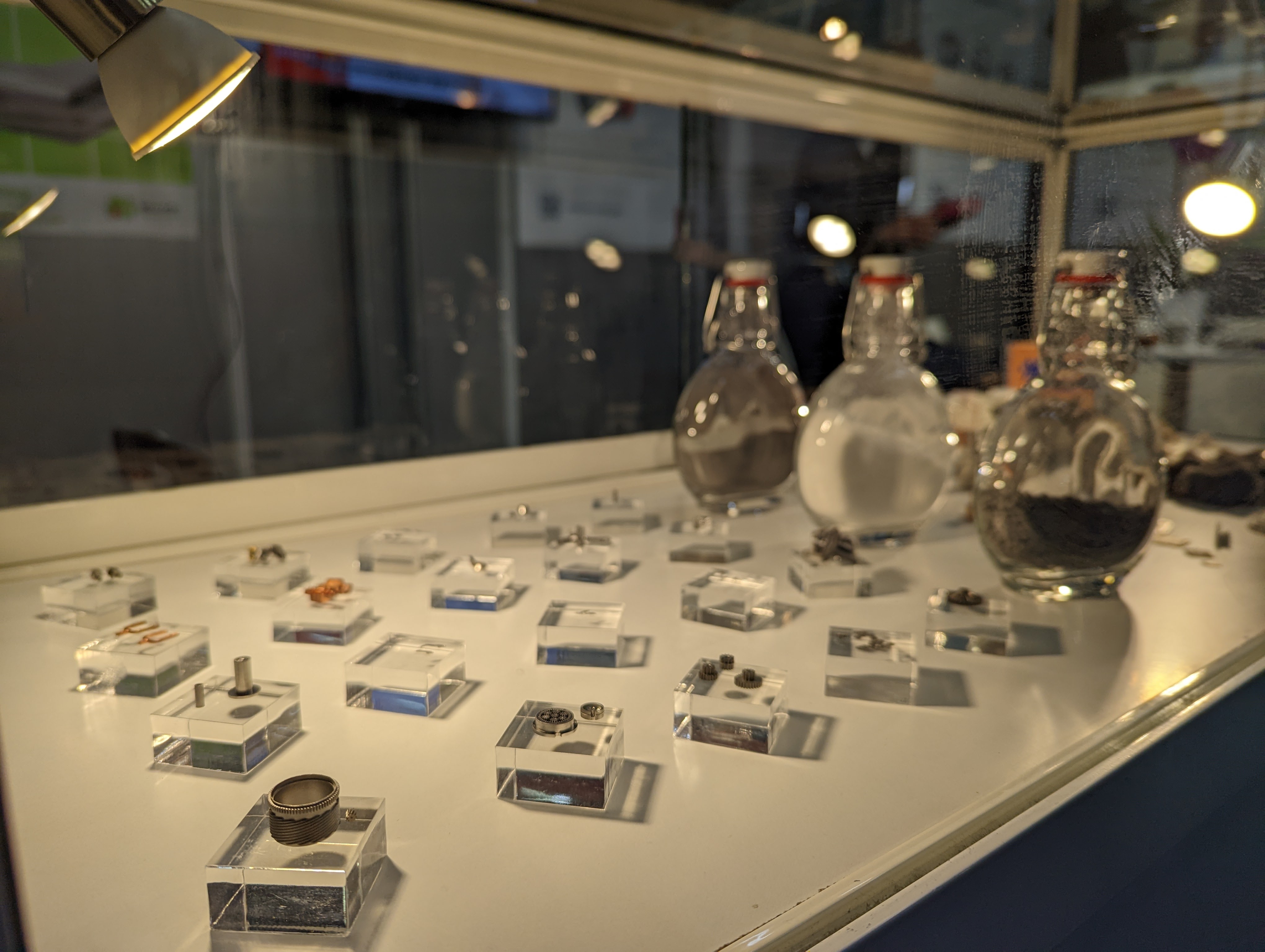
We will be exhibiting at MD&M West 2023 at the Anaheim Convention Center, Anaheim, California, USA from February 7 to 9, 2023. Please visit us at the Booth 629 in Hall E to ask us about your medical device metal parts or to see our sample parts. We look forward to meeting you all soon!
Meet the German team

Christmas is just around the corner and now you can visit Christmas markets all over Germany. During the Christmas season, families, friends and colleagues after work gather at a Christmas market in the evenings many times for a drink and a chat. Glühwein is a classic drink that people would have, and you can easily buy freshly grilled sausages and German potato pancakes and so on. This year, we celebrated upcoming Christmas and the end of the year at the Christmas market and at a very nice Japanese restaurant in Düsseldorf, Germany. We wish you all happy holidays and a good start in a great year 2023!
Download the PDF file
Conclusion
Cracking, slumping or blistering is commonly observed due to the binder swelling and/or residual stress difference between the surface and interior. It is possible to avoid these problems by selecting appropriate organic solvents and temperature control.
The catalytic deboning uses sublimation of binder, thus it is possible to decompose the binder in relatively short processing time with minimizing the deformation. However, with a strong acidic atmosphere, theapplicable metal material option is limited.
In the sintering process, the necking, which is bridging the metal powders by thermal diffusion, starts at the sintering temperature. Once the necking starts, the shrinking is observed and increases the density, thus before starting the necking reaction, all the organic components should be decomposed and gas between the powders should be removed. In the sintering process, the unwanted chemical reaction, such as oxidation or carbonization, leads to mechanical property loss, therefore a precise atmosphere control with low heating rate at the beginning of the process is required. Also, when it reaches the sintering temperature, some add it vegetal can be evaporated.